Gestion d’entrepôt : bien organiser et gérer un entrepôt permet de posséder du stock nécessaire, de fournir le meilleur service, d’augmenter le pourcentage d’occupation, de réduire le temps réservé aux activités internes comme le transport ou le picking, de surveiller le stock, ainsi que d’optimiser les emplacements et les flux..etc.
L’entrepôt idéal est intelligent, c’est à dire, sa gestion est logique et efficace, et ce pour obtenir la performance maximale possible.
Aujourd’hui, il n’est pas possible d’établir une installation professionnelle sans logiciel de gestion d’entrepôt (Warehouse Management System – WMS), pour assurer un bon fonctionnement, comme c’est mentionné au début de cet article.
Le choix du WMS efficace est primordial et permettra de faire, simplement et intuitivement, les fonctions de base de gestion d’entrepôt.
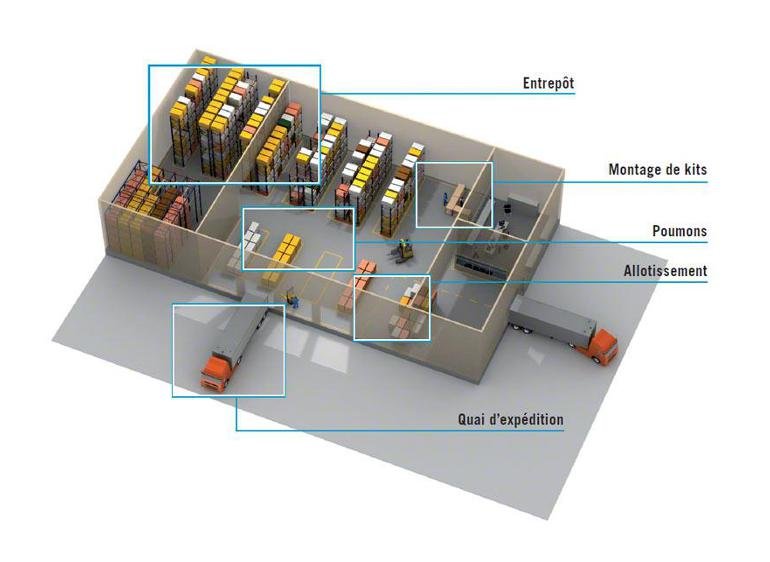
I. Par qui l’entrepôt est-il géré ?
La plupart des entrepôts sont gérés de façon directe par l’entreprise qui est propriétaire de l’installation. Toutes les fonctions du système peuvent s’intégrer, se rattacher ou se coordonnent avec le management de l’entreprise.
Le WMS ne peut être appliqué qu’aux fonctionnalités spéciales de l’entrepôt et par l’intermédiaire d’un ensemble d’interfaces, en mettant en place une communication temps réel avec le système de gestion global/central de l’entreprise.
Néanmoins, les entreprises externalisent de plus en plus intensément les services logistiques et de stockage via des prestataires qui, outre le stockage, offrent des solutions complètement intégrées, en préparant le picking, en installant des composants, en prenant en charge le transport..etc.
Alors là, l’entrepôt d’un prestataire logistique peut contenir des stocks de plusieurs clients (ou propriétaires), qui devront être gérées de façon correcte. Dans cet exemple, le WMS doit être susceptible d’être utilisé selon le concept de multipropriété.
Comment gérer la marchandise et son stockage ?
L’établissement de la gestion d’entrepôt doit se précéder d’une analyse fonctionnelle. Cette analyse traite les flux de matériels, prend en considération les caractéristiques et le type d’installation, et ses composants.
Pour stocker la marchandise dans l’entrepôt, il faut considérer le classement des produits A-B-C et placer les produits A dans les emplacements les plus proches et les plus accessibles.
Le critère considéré pour le stockage sur rayonnages adapte la méthode de travail et la capacité effective. On peut citer trois méthodes de stockage pour identifier la position de chaque unité de charge.
- Pour la méthode de stockage spéciale ou fixe, un ou plusieurs emplacements définis à l’avance est affecté à chaque référence. Le grand avantage de cette méthode se manifeste dans la facilité d’affectation de localisation des références. Les employés qui travaillent dans l’entrepôt savent où se trouve chacune d’elles sans avoir besoin d’une assistance informatique. Son inconvénient le plus clair existe dans la perte de capacité effective, qui est très faible par rapport à la capacité physique (nombre d’emplacements). Cette façon de stockage ne doit être utilisée que dans des entrepôts de petite taille, qui n’a pas besoin d’un système de gestion.
- Avec la méthode de stockage aléatoire, nommée aussi méthode chaotique, libre ou variée, la marchandise est stockée dans n’importe quel emplacement libre disponible, selon une logique établie et programmée d’avance dans le WMS. Le classement A-B-C est généralement pris en considération. Le système dans lequel toutes les données ont été intégrées (y compris les emplacements libres), montre à l’opérateur l’emplacement où il doit déposer ou prélever la marchandise. Outre la gestion parfaite que cela implique, la méthode de stockage chaotique assure une capacité effective qui peut s’élever à 92 % de la capacité physique de l’entrepôt, si ce n’est pas le cas.
- La dernière, la méthode de stockage mixte ou semi-aléatoire est la plus intensément utilisée. Elle regroupe méthode spécifique et méthode aléatoire selon le type de produit ou de l’opération à faire. La méthode de stockage spécifique est donc utilisée pour des produits très consommés, généralement mis à côté des quais ou des zones de picking, alors que la méthode de stockage aléatoire est appliquée pour les autres produits et les zones de réserve.
La gestion des emplacements, notamment dans des systèmes de stockage spécifique, suit des paramètres de productivité par l’intermédiaire de l’optimisation des parcours, en particulier ceux utiles à la préparation des commandes.
Outre le choix de la méthode adéquate, il est indispensable de posséder un WMS qui correspond à chaque cas.
II. L’entrepôt central
L’entrepôt central, en plus du stockage des produits définis, qui sont obtenus par un ou plusieurs processus industriels et qui, par conséquent, ont une ou plusieurs origines, joue le rôle d’un centre de distribution pour ces derniers.
Inversement aux centres de distribution, l’entrepôt central fait l’expédition presque exclusive des produits stockés à d’autres entrepôts sur le plan régional ou local, pour les approvisionner.
Ils seront donc à leur tour collectés de la distribution finale vers les consommateurs.

Ainsi, l’entrepôt central sert de réserve. Cependant, on n’a pas toujours besoin d’adopter cette stratégie, tout revient au produit et à la rapidité de livraison.
Si on a un bon service de livraison, à un prix concurrentiel, à partir d’un entrepôt central dûment dimensionné, on pourra livrer n’importe quel article à n’importe quel client.
L’entrepôt central est donc l’un des éléments indispensables d’un réseau de distribution, c’est pour cela il fallait bien approfondir les questionnements relatifs à la stratégie, au mode opératoire et à la fonction d’un centre de ce type.
1) Critères déterminant le choix de l’emplacement d’un entrepôt
Parmi les points importants de l’installation d’un centre de ce type est également le choix de sa localisation.
Ce choix doit reposer sur un équilibre entre la localisation des sources d’approvisionnement en matériaux ou produits, et l’emplacement territorial des centres de distribution ou des clients qui vont recevoir les marchandises.
2) Influence de la localisation des sources d’approvisionnement
L’emplacement d’un entrepôt central doit être sélectionné selon sa source d’approvisionnement :
-Si la source d’approvisionnement est unique, comme le cas d’une installation programmée pour l’expédition de produits laitiers préparés dans une usine adjacente, il s’agit de l’entrepôt central d’une usine et il est tout à fait normal qu’il soit intégré dans celle-ci ou implanté à côté.
-S’il y en a plusieurs sources, tel l’entrepôt central d’une série de magasins de vêtements qui accueillit des articles issus de différents fabricants, il fallait bien l’installer en un point stratégique vis à vis l’emplacement des sources d’approvisionnement.
3) Influence de la situation des points de destination
L’état des points de distribution auxquels est planifiée la marchandise manipulée par un entrepôt central est moins déterminante pour le choix de la localisation de ce dernier que celle des sources d’approvisionnement.
Généralement, les deux fonctions que doit fournir un entrepôt central sont le conditionnement, et la préparation du produit pour la phase suivante de la chaîne de distribution.
Ainsi, pour le produit, le transport vers un autre centre de distribution pose moins de risques que le transport depuis le site de production. C’est pour cela la localisation des centres secondaires importe moins que celui de l’entrepôt principal.
Le seul caractère à mettre en évidence est le choix d’un site relié comme il faut au territoire et accessible aux moyens de transport disponibles.
L’entrepôt central possède un rôle de centre de distribution, car il peut expédier les produits vers d’autres entrepôts régionaux ou locaux.
III. Rôles de l’entrepôt
Un entrepôt central bien établi doit avoir la capacité d’exécuter les fonctions suivantes :
-Réception de tous les produits intégrés dans l’activité industrielle de l’entreprise propriétaire de l’entrepôt.
-Réalisation d’un contrôle qualité immédiatement.
-Surveillance et inventaire des stocks.
-Organisation du stockage préalablement.
-Préparation des commandes qui seront envoyées aux entrepôts régionaux et/ou aux clients.
-Diffusion rapide des commandes.
Alors là en quoi consiste chacune d’entre elles à votre avis ?
1) La réception des produits
Pour réaliser efficacement l’expédition de la marchandise qui vient de l’activité industrielle de la société possédant un entrepôt central, un ensemble d’actions préalables sont indispensables afin de définir les moyens techniques, humains et informatiques nécessaires.
Tout commence par le taitement exhaustif des produits arrivés au centre. Ce traitement doit bien considérer les dimensions et le poids des unités de charge, de la dureté de l’emballage, du rythme des arrivées du matériel et de la quantité de marchandises réceptionnée.
Le poids et les dimensions des produits réceptionnés
Le traitement de ces deux leviers adapte les besoins à couvrir les marchandises reçus. Ainsi, les caractéristiques des marchandises receptionnées, les modes de stockage et, le type et les capacités de charge des engins doivent être bien assurés.
Les engins de manutention doivent être bien conditionnés à la manutention de la marchandise lors de la réception, et, le cas échéant, pour l’expédition.
Les marchandises reçus peuvent avoir des formes, des tailles et des poids différents. D’ailleurs ces variables interviennent dans la plupart des cas, et plus les sources d’approvisionnement sont diversifiées, plus cet état est fréquent.
En général, deux situations se manifestent : soit les unités détiennent les dimensions et le poids convenables pour être stockées de façon directe, soit une partie d’entre elles n’ont pas ces critères et doivent être substituées avant le stockage.
Dans ces deux cas, l’entrepôt central doit être prêt pour la réception, la préparation et le stockage de tout type de marchandises, et, pour le faire, un ou plusieurs quais doivent être aménagés ainsi qu’une partie d’accueil et, le cas échéant une partie d’expédition, mais aussi en disposant des engins de manutention pour faire la décharge des camions.
Les engins ou les outils mécaniques en général pour simplifier le chargement/déchargement des marchandises sont les transpalettes, les gerbeurs et les chariots élévateurs à contrepoids..etc.
2) Le contrôle qualité
Le contrôle qualité élaboré dans un entrepôt central est limité à le fait de s’assurer que le contenu de la charge receptionnée est correspondant à celui qui convient avec le fournisseur.
Pour faciliter cette opération, les unités de charge doivent être associées à un bordereau de livraison qui indique les critères du produit receptionné, sa dénomination commerciale en cas de besoin, et la quantité d’unités que contient chaque conditionnement/emballage (palette, conteneur, caisse…).
Utilisant ce bordereau, le personnel qui réçoit la marchandise est appelé à faire un échantillonnage sélectif, ouvrir un conditionnement, le cas échéant, et en vérifier le contenu.
Ce contrôle est établi pour vérifier la quantité et la qualité de la marchandise receptionnée.
Le contrôle qualité assure notamment la vérification si le conditionnement est suffisamment résistant pour supporter la durée de temps et les conditions de stockage prédéfinies.
Le cas échéant, l’emballage doit être modifié pour l’adapter aux caractéristiques de l’entrepôt; cette action est surtout réalisée dans les entrepôts centraux qui receptionnent des marchandises des fournisseurs/sources différents.
3) Le contrôle et l’inventaire des produits stockés
Directement après le contrôle qualité, un comptage des produits doit s’effectuer. Ensuite, les données sont saisies dans un ordinateur central.
Le département qui se charge des réceptions doit posséder un ou plusieurs terminaux afin de présenter tout de suite une réclamation au centre de fabrication ou au fournisseur approprié s’il remarque une divergence entre la marchandise et le bordereau
à savoir que l’intégration des données doit être faite après le comptage, et pas avant, toujours.
Une fois les unités de charge intégrées, le système communique la localisation exacte affectée à chaque unité, comme indique la programmation de stockage prédéfinie.
Lors de l’opération d’expédition des marchandises, l’opération inverse est réalisée en indiquant à l’ordinateur la sortie des unités adéquates; donc, le système de gestion peut posséder de l’emplacement libre et lui affecter une nouvelle unité de charge.
La sortie de la marchandise ne doit être sauvegardée qu’au bon moment où l’opération est réalisée car, si l’ordinateur va créer un bordereau, pendant le temps qui sépare l’émission de ce document et le prélèvement effectif de l’unité, son emplacement doit se présenter comme occupé.
Contrairement, le système pourrait considérer que la localisation est libre et lui affecter une nouvelle unité de charge.
Si la marchandise qui précède n’a pas encore été prélevée, l’opérateur va trouver l’alvéole occupée, cas qui peut se manifester si l’entrée et la sortie de marchandises se font à un rythme différent.
Pour éviter tou ça, l’ordinateur ne tient pas compte l’emplacement comme vide tant que l’opérateur n’a pas prélevé l’unité et diffusé l’opération au système.
L’utilisation d’un logiciel de gestion d’entrepôts (WMS) spécialisé assure le bon fonctionnement de toutes les étapes en question dans cette opération, et évite les erreurs de gestion des localisations.
4) L’organisation préalable du stockage des marchandises
Les entrepôts centraux doivent avoir des moyens mécaniques qui suffisent et utiles pour le stockage des marchandises.
Si elles sont reçues sur palettes, il faut avoir des moyens ou des engins de manutention pour les manipuler de manière correcte et en toute sécurité, puis les emplacer dans la zone de stockage.
Si la marchandise est arrivée en vrac, il faut non uniquement avoir des moyens obligatoires pour sa manutention, mais aussi, peut être, des outils ou des machines nécessaires à son conditionnement.
Pour faire ça, on peut utiliser une trémie par exemple, tout autre outil mécanique qui convient, si le volume et les caractéristiques de la marchandise le nécessitent.
Généralement, il n’est pas possible d’établir un stockage correctement, ou d’espérer avoir une installation à grande rentabilité et efficacité, si on ne la dote pas des moyens physiques, humains et matériels qu’il faut.
5) La préparation de commandes destinées aux entrepôts régionaux
Comme déjà énoncé, l’une des missions les plus importantes d’un entrepôt central est de servir de réserve aux sites régionaux ou locaux, aussi la fonction importante qu’il doit exécuter est la préparation de commandes passées par ces derniers.
Cette opération peut s’exécuter avec une fréquence quotidienne, hebdomadaire, mensuelle ou bimestrielle (voire plus espacée) selon la périodicité appropriée, des éventuels produits utilisés et de leur taille.
La section suivante traite les différents modes et méthodologies utilisés pour préparer les commandes.
Tous sont élaborés pour des cas réels, et leur choix se fait en fonction des besoins spécifiques de chaque entreprise.
Aussi, on peut souligner que pour qu’un entrepôt central puisse réaliser efficacement la préparation de commandes, il est nécessaire d’aménager des espaces à cet effet sur les rayonnages ou au sol, et pour faire ça, le stockage doit être efficacement organisé.
Normalement, la préparation de commandes dans un entrepôt central est réalisée au sol ou au moyen de systèmes automatiques ou semi-automatiques. Cela augmente la capacité de stockage, et, accélère et simplifie les opérations.
On peut obtenir ces avantages via deux facteurs principaux :
- La possibilité de remplir totalement les espaces libres des rayonnages, ce qui augmente évidemment la capacité de stockage par rapport à la préparation sur rayonnages dans laquelle la (ou les) localisations réservées à cette opération sont la majorité du temps à moitié vides.
- Deuxièmement, le sol est le niveau optimal pour préparer les commandes, car il assure la multiplication de la rentabilité tout en accélérant les opérations, et en réduisant le risque de fautes.
Par ailleurs, la préparation de commandes par des systèmes automatiques ou semi-automatiques réduit le temps réservé à ces opérations.
Mais pour atteindre le meilleur rendement possible, les commandes doivent être efficacement programmées, et, c’est pour cela il est très intéressant qu’elles soient établies, si c’est possible, par unités de charge complètes.
Un autre facteur qui a une influence sur la vitesse et l’efficacité est la capacité de l’entrepôt central à identifier continuellement les besoins des sites secondaires de la chaîne et à prévoir leurs demandes.
Comment mettre en place ces prévisions ? Le moyen efficace et unique est la diffusion des informations ; plus celle-ci est rapide, plus les informations seront précises et meilleurs seront les résultats.
C’est pour cela, la mise en œuvre d’une communication en temps réel entre tous les maillons de la chaîne est obligatoire, du point de consommation finale le plus loin (par exemple, le commerce de détail) jusqu’à l’ordinateur central du site de production ou d’enlèvement.

Ci-dessous un modèle de liaison entre les différents points fournissant des informations : la communication entre l’entrepôt régulateur et l’écran de commandes se fait via l’opérateur grâce à des terminaux RF qui diffusent les informations par des ondes radio.
Finalement, la liaison entre l’entrepôt régulateur et l’écran de commandes est effectuée d’un ordinateur à un autre par l’intermédiaire d’un routeur.
Le système se dispose de plusieurs options et il y en a d’autres possibilités. Les entreprises spécialisées dans les nouvelles technologies de l’information et de communication (NTIC) sont les plus susceptibles à trouver les solutions et à établir les communications qu’il faut.
En outre, pour arriver à tout maîtriser, un logiciel efficace de gestion d’entrepôts (WMS) est obligatoire.

6) L’expédition rapide des commandes
Le délai d’expédition des commandes est basique pour éviter les retards et les ruptures de stock dans les chaînes de distribution.
C’est pour cela l’une des fonctions d’un entrepôt central est d’exécuter rapidement cette opération.
La rapidité d’expédition dépend de la bonne organisation des opérations expliquées précédement. Si elles sont bien exécutées, l’expédition des marchandises commandées sera simple et rapide.
Néanmoins, si l’une des étapes n’est pas bien exécutée, un goulot d’étranglement peut se créer et, l’expédition des commandes risque de devenir compliquée et subir du retard.
La responsabilité principale d’un chef d’entrepôt est ainsi d’essayer à faire une meilleure coordination des opérations à l’intérieur de l’installation.
⛔ Pour devenir un leader inspirant dans votre organisation et maîtriser les compétences et les techniques de leadership avec des conseils très pratiques, je vous propose ces formations qui sont les plus vendues sur Udemy :
✅Leadership: les 48 nuances du pouvoir (de pigeon au faucon)
✅Leadership: Les 20 secrets de la russite en entreprise
✅Leadership devenez un leader inspirant
✅Comprendre et utiliser la méthode EBIOS Risk Manager
✅Management du transport international et de la logistique
✅Comment activer une nouvelle dynamique d’quipe ?
✅Comment motiver et dynamiser une équipe ?
✅ Formation en Management & Leadership – avec la mthode SCRUM
✅ Gestion de projet Agile: Scrum et Kanban
✅Conduite agile du changement : accompagner vos projets
✅100% réussite pour la Certification Scrum Master PSM1