Quels outils utiliser pour améliorer la qualité dans l’entreprise ? Comme tous les services, la fonction qualité a ses outils spécifiques pour gérer et développer le système.
En observant de plus près, ce n’est pas correct de parler de ses propres outils car il en partage quelques uns avec d’autres départements :
Les études de satisfaction avec le marketing (baromètre NPS par exemple), les méthodologies adoptées pour résoudre les problèmes avec les chefs de projet..etc.
Cette fonction n’a pas obligatoirement “réinventé la roue” mais a pu trouver les bons outils pour traiter des problèmes bien précis.
I. AMDEC : définition et mise en œuvre
Aux années 1940 est inventée la méthode AMDEC par l’armée américaine et utilisée par les industries. S’intégrant dans une procédure de prévention, cette méthode est un acteur indispensable au bon fonctionnement de l’entreprise.
1. Qu’est-ce que l’AMDEC ?
AMDEC veut dire “Analyse des Modes de Défaillances, de leurs Effets et de leurs Criticités”. C’est la traduction en français de la méthode FMEA : Failure Mode, Effects, and Criticality Analysis.
C’est une méthode d’analyse qualitative et quantitative qui permet de présenter les faiblesses potentielles d’un produit quelconque, procédé (ou process) en déclenchant des actions de correction ou de prévention.
2. Les types d’A.M.D.E.C
Il existe plusieurs types d’AMDEC, dont les trois plus importants sont :
-AMDEC Produit : c’est l’étude des faiblesses des produits, issues de sa conception, sa création ou son exploitation, pour améliorer sa qualité et son efficacité.
-AMDEC Processus : c’est l’analyse des faiblesses au niveau des méthodes de production d’un produit ainsi que les démarches mises en place pour achever une tâche quelconque.
-AMDEC Moyens de Production : c’est l’étude des faiblesses des machines et équipements contribuants à la création d’un produit.
Vous pouvez notamment trouver des AMDEC de type sécurité, fournisseur, service..etc.
3. Les définitions liées à l’AMDEC
Pour comprendre cette méthode, il est intéressant de connaitre les termes qui lui sont associés.
*Le mode de défaillance : c’est la façon avec laquelle le fonctionnement du système peut s’arrêter, s’écarter des caractéristiques prédéfinies, fonctionner de façon anormale..etc. Il s’exprime physiquement.
Par exemple : fuite, court-circuit, déformation..etc.
Rechercher la défaillance veut dire poser les questions :
-Qu’est-ce qui ne fonctionne pas ?
-Qu’est-ce qui a arrêté de fonctionner ?
-Est ce qu’il y a quelque chose qui s’est dégradé au niveau du fonctionnement global du système ?
-Est ce que le fonctionnement est précoce ?
*La cause de la défaillance : c’est l’anomalie qui peut provoquer la défaillance.
*L’effet de la défaillance : ce sont les conséquences qui impactent l’utilisateur.
*La criticité : elle détermine l’acceptabilité de la situation par plusieurs facteurs fusionnés. Selon son activité ou celle du chef de projet, la méthode de cotation peut différer.
4. La méthode AMDEC en huit étapes
Cette méthode fait partie d’une démarche en huit étapes comme suit :
étape 1 : Construire le groupe de travail
Cette étape représente la construction du groupe de travail. Chaque membre de ce groupe doit avoir préalablement une idée minimale sur la méthode AMDEC et doit venir de plusieurs sources pour mettre en commun les compétences disponibles et d’être dans un processus constructif.
étape 2 : Définir le périmètre de l’étude
En amont, il est important de connaitre et de comprendre le produit, procédé ou processus traité pour déterminer la zone de votre étude et pouvoir l’étudier. Vous pouvez trouver ces informations grâce à une analyse fonctionnelle, dont les questions principales sont :
-Quelle est la fonction d’usage ?
-Quelles sont les fonctionnalités prévues ?
-Y a t-il des contraintes ?
-Quelles sont les fonctions techniques ?
On peut utiliser les outils de l’analyse fonctionnelle : démonstration des besoins, expression fonctionnelle, structuration hiérarchiquement les fonctions, mise en place des cahiers de charges fonctionnels..etc.
Pendant cette étape, les buts et les limites de l’étude sont déterminés.
Cette phase est primordial pour commencer une AMDEC. En ayant peu d’informations concernant son sujet, vous pouvez rencontrer les risques de s’éloigner de la cible et les conséquences peuvent être erronés.
étape 3 : Identifier les modes de défaillances
Une fois ce périmètre défini, vous pouvez identifier les modes de défaillances potentielles en vous posant la question « Qu’est-ce qui peut mal fonctionner ? ».
à partir d’ici, on peut remplir la grille d’analyse. L’objectif de cette phase est d’identifier les défaillances premières et non les causes radicales.
étape 4 : Identifier les effets et les causes
Pour chaque mode de défaillance, déterminez les effets associés à partir de la question « Quels sont les effets et les causes associés à ce mode de défaillance ? »
Evitez d’avoir des limites, vous pouvez rencontrer une ou plusieurs causes et effets par mode de défaillance.
étape 5 : Evaluer les défaillances
Cette phase quantitative permet d’affecter à chaque défaillance potentielle un indice de criticité. La criticité vient de la fusion de 3 facteurs :
-la gravité de la défaillance et de l’effet (G) : résultat plus ou moins grave pour l’utilisateur ;
-la fréquence d’apparition de la défaillance, l’occurrence (O);
-la possibilité de non-détection (D) : la défaillance se produit et il y a un risque de ne pas pouvoir l’identifier.
Vous devez déterminer une échelle pour chaque facteur. Vous pouvez trouver une échelle allant de 1 à 4 ou de 1 à 10. 1 est une gravité/occurrence/probabilité faible et 10 est une gravité/occurrence/probabilité forte.
Pour pouvoir analyser les défaillances, il est intéressant de bien déterminer l’échelle et d’y introduire des critères pour chaque point.
Par exemple, sur une échelle allant de 1 à 4, vous pouvez déterminer une fréquence d’apparition selon les aspects suivants :
1 : Annuelle ou plus
2 : Trimestrielle/Mensuelle
3 : Hebdomadaire à quotidienne
Plus vous soyez précis dans vos critères, plus il sera facile d’appliquer une notation en se rapprochant de la réalité.
étape 6 : Hiérarchiser les défaillances
Après avoir réalisé ce calcul, on peut ordonner les défaillances par ordre de priorité en fixant des limites d’alerte pour réaliser le traitement des données par ordre prioritaire.
Ci-après un exemple de différentes limites d’alerte en se basant sur une cotation allant de 1 à 4 :
-37 – 64 : criticité majeure
-28 – 36 : criticité importante
-10 – 27 : criticité mineure
-1 – 9 : criticité faible
Ce résultat permet donc de traiter prioritairement les défaillances qui ont une criticité majeure, puis importante, et ainsi de suite.
étape 7 : Rechercher des solutions
Après le classement des divers modes de défaillance, vous aurez 2 solutions :
-supprimer la défaillance
-réduire la défaillance
Dans le 2ème cas, on peut chercher des solutions par procédures de correction et/ou de prévention afin d’avoir une criticité plus faible de l’occurrence/la probabilité de non-détection/la gravité. Pour chaque procédure/action, on doit désigner un manager.
étape 8 : Suivre les actions
Le but est de vérifier l’efficacité des solutions qui ont été choisies et de réévaluer la criticité, pour assurer que cette dernière a bien été réduite. Ce suivi est intéressant, car il aide à définir l’efficacité et l’influence des actions qui ont été réalisées.
5. Les limites de l’AMDEC
La méthode AMDEC peut paraitre compliquée. Elle exige une bonne organisation et engagement du groupe de travail et de rester précis dans la procédure et les recherches.
6. En synthèse
L’AMDEC a comme objectif la satisfaction du client par le fait de prévenir des défaillances sur tous les plans de la conception participant alors à l’amélioration de la qualité et de l’efficacité du sujet traité.
C’est une méthodologie pertinente pour effectuer une analyse préalable des risques d’un produit, améliorer en permanence l’organisation de l’entreprise.
L’objectif est la prévention. Cette méthodologie d’amélioration continue génère une liste structurée de points faibles qui permet de distinguer un équipement de production d’un autre.
L’AMDEC ne permet pas seulement de faire le diagnostic des systèmes qui fonctionnent, elle s’applique dès la conception pour anticiper les éventuelles défaillances.
L’essentiel, il faut être en mesure d’ajouter des corrections très tôt avant le déclin du dispositif.
Les pratiques de la méthode ne sont pas limités aux moyens techniques (équipements), les process et les procédures profitent également de ses vertus .
La méthodologie demande une compréhension du système concerné, d’autres moyens comme l’analyse fonctionnelle ainsi interviennent.
On peut étudier les effets des modes de défaillance, pour les structurer hiérarchiquement par la suite. Cet outil est au centre de plusieurs pratiques qualité.
II. Les 5S : Seiri, Seiton, Seiso, Seiketsu, Shitsuke
La qualité totale propose plusieurs outils pour aider les organisations à s’améliorer. La méthode 5S est un élément de cet ensemble en édictant des règles qui assurent l’amélioration de son lieu de travail.
à la clé : bonne organisation des locaux, clarté et propreté. Des enjeux importants pour assurer des conditions de travail favorables, sécurisées et ayant une image reflétée à l’extérieur agréable.
1. Définition : ce qu’il faut savoir
La méthode 5S provient de 5 verbes japonais montrant les tâches principales à réaliser pour améliorer son entourage de travail.
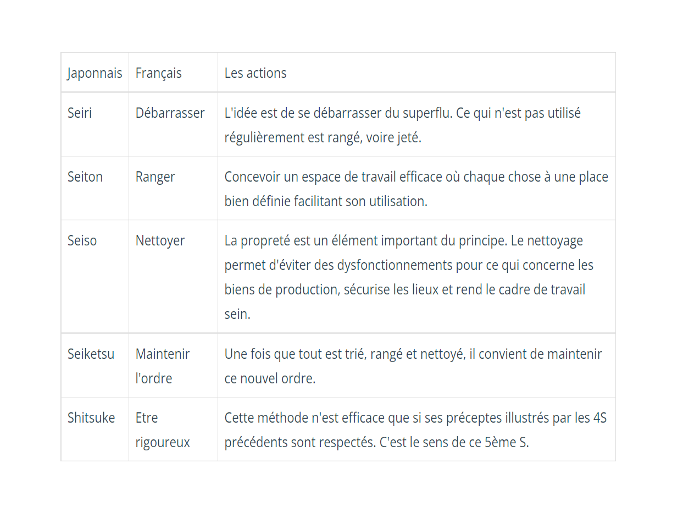
L’ordre des actions est intéressant. On commence par débarrasser ( Seiri) pour finir en maintenant de la précision concernant les bonnes pratiques récemment acquises (Shitsuke).
2. Les enjeux
Un lieu de travail optimisé où l’ordre est indispensable, on peut trouver les documents de façon plus facile et rapide sans perte..etc.
Cet environnement permet d’accélérer le travail sans se perdre des fonctions sans aucune valeur ajoutée, de réduire le nombre d’accidents de travail (dans le cas des ateliers) et de se focaliser sur l’essentiel.
3. Applications de la méthode 5S
Créé spécialement pour organiser les ateliers de production, cet outil est aujourd’hui utilisé pour optimiser tous les espaces professionnels.
Tout d’abord, les bureaux. On peut l’appliquer à toutes les catégories d’entreprise, peu importe sa taille ou son domaine d’activité. Même au niveau des services.
4. Mise en oeuvre d’une opération 5S
On commence tout d’abord par une formation de cinq étapes. Une phase intéressante pour comprendre ce que les employés vont devoir faire ensuite.
Les managers mettent en place des règles et principes de rangement : réservation des zones de stockage, les outils de classement disponibles, voire même annuler les objectifs.
Pour faciliter l’implication de ses salariés, ces actions prennent souvent la forme de “grandes messes” pour mettre en place une certaine émulation.
III. Diagramme de Kano
Le diagramme de Kano, l’outil conçu par Dr. Noriaki Kano pendant les années 1980 a pour objectif d’évaluer la satisfaction client.
Le côté originalité de l’approche apparait dans la distinction de la satisfaction et de la non satisfaction vis à vis la présence ou l’absence de la fonction souhaitée par le client.
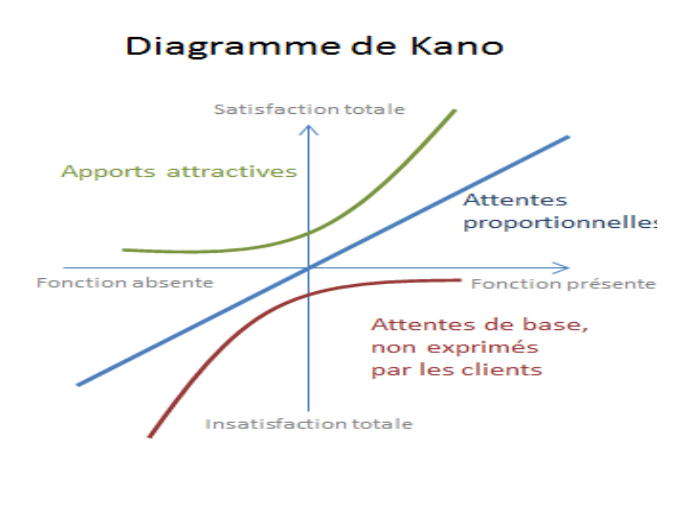
L’analyse donne naissance à 3 positionnements essentiels sur la courbe de Kano :
1- Les attentes basiques : souvent non explicites, les fournisseurs doivent obligatoirement les satisfaire pour garder sa place dans le marché.
2 – Les attentes proportionnelles : la satisfaction augmente proportionnellement avec le degré de performance fourni par la fonction.
3 – Les attentes attractives : le fournisseur essaye de surprendre ses clients avec une fonction à valeur ajoutée qu’il n’a pas attendu auparavant. Les fonctions dépassent les attentes des clients. C’est un terrain favorable pour l’innovation.
Pour mettre en place ce diagramme, un questionnaire Kano receptionne, pour chaque fonction, le degré de satisfaction de l’interlocuteur.
La méthode représente l’évaluation de façon successive de la satisfaction d’un côté si la fonction est présente et d’autre côté si elle est absente.
Que faut-il attendre de cette méthode ?
-Elle assure l’évaluation des attentes des clients par l’intermédiaire du niveau de satisfaction associé.
-Elle aide à faire l’évaluation des produits notamment les produits innovants.
Finalement, même si la démarche est plus ou moins dure à gérer, elle envisage l’avantage d’établir une rencontre avec ses clients et développer ainsi la compréhension des besoins de son marché.
IV. Savoir utiliser la roue de Deming
Le PDCA (Plan – Do – Check – Act) est un outil très utile au niveau de la qualité. Ses lettres de noblesse sont issues des démarches ISO 9001.
1. Définition de la roue de Deming
Elle inspire ses bases de l’amélioration continue. Le principe est une roue infinie qui permet à l’entreprise de s’améliorer continuellement.
Au-delà des usages clairs, cet outil, ou même est ce qu’on peut dire que cette méthode, est applicable à plusieurs problèmes managérials.
Cela ne vous rappelle-t-il pas la procédure marketing , ou le cycle de veille…? Il s’agit d’une démarche logique de réflexion-action très connue en management.
2. Comment utiliser le PDCA ?
Il fallait bien suivre les préceptes de Deming :
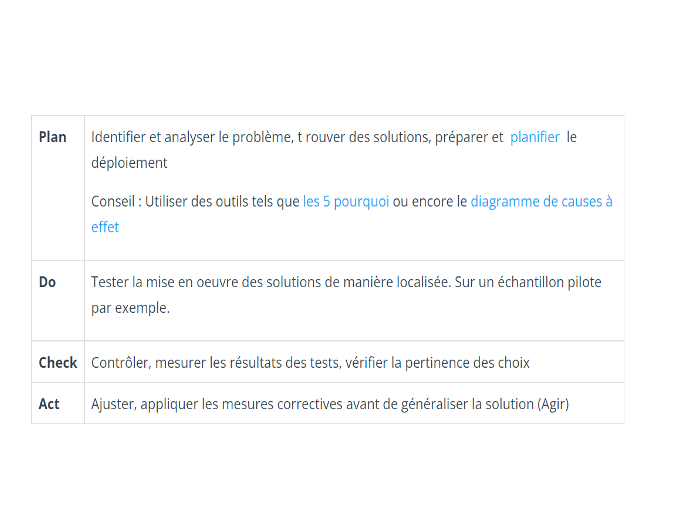
Remarque : dans plusieurs cas la phase de test du Do est substitué par une mise en place plus générale. Le “Check” et le “Act” étant dans cette situation une revue des solutions / actions mises en œuvre.
Si le “Do” ne représente pas de problèmes particuliers, le “Plan” et encore plus le “check” sont généralement “les parents pauvres” des actions à réaliser.
En effet, plusieurs entreprises passent rapidement à la phase terrain avant qu’une analyse complète du problème et une planification suffisante soit mises en place.
De même que la phase de contrôle/suivi est généralement réalisée formellement pourtant la mise en place du plan d’action peut exiger une modification bénéfique pour son propre succès.
V. Six sigma : définition de la méthode et mise en oeuvre
Le Six Sigma fait partie du Lean Management et du processus d’amélioration continue, au même titre que le Kaizen, le Kaban ou le Juste-à-temps. Découvrons ensemble cette méthode assez puissante.
Le Six Sigma est apparu aux années 1980 par Motorola et a été mis en œuvre dans les grandes industries environ 10 ans plus tard.
Pour les entreprises qui appartiennent à l’ère de l’excellence opérationnelle, cette procédure permet de rechercher l’efficience et l’optimisation au niveau de son organisation.
Définition du Six Sigma
Il s’agit d’une démarche de management et d’amélioration des procédures. Le Six Sigma repose sur l’usage statistique des données permettant d’analyser et gérer les facteurs opérants sur un process.
L’objectif est de diminuer le nombre des causes de variabilité afin d’améliorer la qualité et l’efficacité des produits (et des services).
Cette approche se conduit sous forme de projet, orientée client et a une grande influence sur le triplet : Qualité, Coût, Délai.
Alors, la finalité du Six Sigma est de développer les performances des démarches de l’entreprise pour garantir une bonne qualité de produits et satisfaire les besoins des clients tout en gardant la compétitivité de l’entreprise.
1. Domaines d’applications
Le Six Sigma peut être appliqué à chaque organisation possédant un système de management opérationnel et une équipe projet qui permet de mettre en œuvre cette procédure.
Une industrie ou une entreprise de service peut bien utiliser le Six Sigma dès que leurs processus soient déjà bien définis et opérationnels.
2. Principes et enjeux du Six Sigma
Le principe principal du Six Sigma est de réduire la variabilité d’un process en activant les deux aspects qui suivent :
-diminuer le taux de dispersion,
-centrer le processus.
Pour avoir ce résultat, il convient de définir préalablement les processus clés de l’entreprise et de posséder les moyens de les mesurer.
Mettre en œuvre la procédure Six Sigma montre un tel intérêt pour les entreprises voulant :
-diminuer le nombre de réclamations clients,
-réduire le gaspillage et les coûts associés aux non-qualités,
-maitriser ses processus,
-développer son image de marque et la satisfaction de ses clients.
Limites
Les limites de cette démarche sont de bien comprendre ses process et de posséder une équipe spécialisée qui fonctionne en mode projet (Green Belt et Black Belt).
3. Méthodologie Six Sigma en cinq étapes
La méthode utilisée pour mettre en œuvre le Six Sigma est la méthodologie DMAIC. Elle est organisée en cinq étapes, représentant le principe de l’amélioration continue.
- Définir le but et le champ du projet
Déterminer une ou plusieurs démarches et construire un groupe de travail avec un chef de projet. L’objectif est de définir les critères recherchés et les conséquences à obtenir.
-Identifier la problématique, l’objectif recherché
-Définir le processus cible
-Identifier les attentes et besoins clientèles
-Créer l’équipe projet
Les moyens utilisés pour cette 1ère étape sont : Voix du client, SIPOC, logigramme, CEM.
- Mesurer, rassembler les informations sur le fonctionnement actuel
Une fois cette zone établie, regrouper les informations pour réaliser l’étude. L’objectif de cette phase est de cartographier la situation actuelle des process qui ont été fixés et collecter des données pertinentes sur lesquelles on va se baser.
-Collecter les données mesurables,
-Créer une base de données avec les attributs collectés,
-Définir l’état actuel du processus.
Outils et moyens à utiliser : cartographie des processus et indicateur de capabilité.
- Analyser les dysfonctionnements
Il est par la suite moment d’assemblage de toutes les informations collectées et d’analyse des résultats.
-Analyser les mesures de la démarche,
-Déterminer les causes du dysfonctionnement.
Parmi les outils qui permettent d’analyser les dysfonctionnements on peut citer : AMDEC , Analyse de données, diagramme de corrélation, plan d’expérience..etc.
- Améliorer, mettre en œuvre des solutions
Après l’analyse, définir des solutions par actions curatives et/ou préventives aidant à réduire la variabilité des process. Chaque action doit être enregistrée dans un tableau de suivi avec un responsable désigné.
-Déterminer les solutions,
-Appliquer ces solutions en actions,
-Insérer ces actions dans un tableau de suivi de plan d’action,
-Affecter un responsable par action.
L’outil utilisé : tableau de suivi de plan d’action.
- Contrôler, maintenir les solutions en pérennisant le travail
Cette dernière étape renforce sa précédente et permet de vérifier que les solutions sélectionnées ont été bénéfiques. Dans ce cas, il est important de rendre les solutions choisies pérennes.
-Concevoir un plan de surveillance,
-Mettre à jour la documentation,
-Créer les ressources,
-Communiquer sur les solutions choisies.
Il est intéressant de se souvenir toujours du maintien et de l’amélioration continue des process et du système de Management.
Les outils qui permettent le suivi de l’efficacité des process : standards, carte de contrôle, indicateurs et tableaux de bord…
4. Les outils
Pour schématiser la démarche Six Sigma et la méthode DMAIC, voici 2 outils de management visuel à utiliser.
L’outil SIPOC est fréquemment utilisé dans la méthode Six Sigma. Il assure le cadrage du processus tout entier :
-Fournisseurs (Suppliers)
-Données d’entrée responsables du bon déroulement du processus (Input)
-Processus : actions donnant lieu aux données de sortie à partir des données d’entrée
-Outputs : données, services ou produit final fournis par le processus
-Customer : membres qui déterminent leurs besoins du produit/service final
La carte de contrôle est un outil qui permet de formaliser et montrer les résultats des observations réalisées. Et donc, comprendre la variabilité du processus analysé :
- Définir le critère à observer.
- Définir le seuil de tolérance qui peut être accepté.
- Formaliser les résultats sur la carte.
- Analyser les résultats obtenus.
- Identifier les causes des critères qui n’entrent pas dans le seuil de tolérance.
⛔ Pour devenir un leader inspirant dans votre organisation et maîtriser les compétences et les techniques de leadership avec des conseils très pratiques, je vous propose ces formations qui sont les plus vendues sur Udemy :
✅Leadership: les 48 nuances du pouvoir (de pigeon au faucon)
✅Leadership: Les 20 secrets de la russite en entreprise
✅Leadership devenez un leader inspirant
✅Comprendre et utiliser la méthode EBIOS Risk Manager
✅Management du transport international et de la logistique
✅Comment activer une nouvelle dynamique d’quipe ?
✅Comment motiver et dynamiser une équipe ?
✅ Formation en Management & Leadership – avec la mthode SCRUM
✅ Gestion de projet Agile: Scrum et Kanban
✅Conduite agile du changement : accompagner vos projets
✅100% réussite pour la Certification Scrum Master PSM1